- Home
- Special Services
MARINE SERVICES
construction
other services
weld services
- NDT Services
methods
additional services
- About Us
- Locations
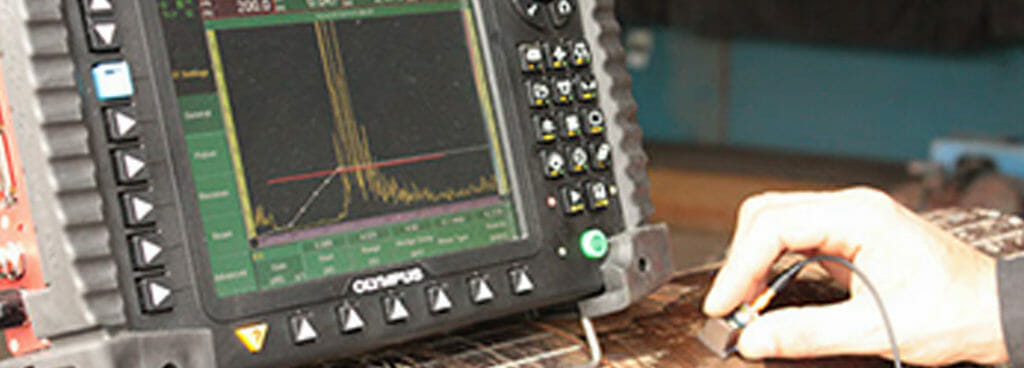
Importance and Applications of Nondestructive Evaluation
International Inspection provides a host of services related to the nondestructive evaluation of client assets. The phrase refers to a branch of testing that reveals any number of characteristics, from physical attributes to elemental composition, without causing damage to the subject being analyzed. It is alternatively known by its acronym (NDE), or as nondestructive testing (NDT), or even as nondestructive inspection (NDI) depending on preference — each term is functionally interchangeable and refers to the same methods of analysis.
Nondestructive evaluation is a critical aspect of any industry’s maintenance plans. By recruiting qualified experts to determine the condition of their assets, they can ensure their long-term functionality. Allowing corrosion- or mechanical-related damage to accrue in industrial machinery can diminish efficiency, undermine productivity, cause unplanned downtime, necessitate costly repairs, or even injure personnel. Reliable examinations performed by experienced inspectors like those from International Inspection equip clients with the insight they need to maintain their assets’ well-being.
International Inspection's NDE Capabilities
We employ a team of ASNT certified Level II and III technicians to perform our various NDT services in accordance with applicable inspection codes. These professionals meet clients onsite and assess the health of their structures, equipment, vessels, and machinery as requested in the scope of evaluation. They complete these inspections using one or a combination of the following methods:
Visual Testing
The most fundamental form of nondestructive testing is the visual assessment of a subject. Our inspectors bring collective decades of experience to every jobsite, examining components for either the presence or indications of damage that can undermine the performance and longevity of an asset. They are talented at identifying areas of interest and investigating them for malfunctions, corrosion, leaks, and other visible signs that something is out of the ordinary. Documenting their evaluation through photos and video allows inspectors to make clients aware of the subject’s condition and recommend maintenance or repair steps to address problematic findings.
Our field team employs this method for the assessment of any type of machinery, structure, vessel, or fabrication as deemed appropriate in the inspection scope. Depending on the areas to be observed, they may supplement this process by using specialized camera systems, such as a borescope for piping or a snake eye camera for areas with access as small as 1.5”.
By noting any causes for concern in their observations, inspectors can notify the client if additional, intensive examination using more incisive methods is warranted; other disciplines of NDE can verify the underlying cause behind an indication of damage or more completely characterize a discontinuity discovered by visual inspection.
Penetrant Testing
Penetrant testing allows International Inspection to see minute flaws — such as forging laps, porosity, and cracks of every breed — in non-porous surface materials. Field technicians begin performing this nondestructive method by applying a penetrant to the surface of a subject and letting it soak into any present defects for an appropriate duration. They then remove excess from the surface, which leaves an amount of penetrant dwelling in the discontinuities. By applying a white developing agent to draw the brightly colored compound back to the surface, technicians can then observe a stark indication of surface faults created by the highly contrasting colors of the two compounds.
Also referred to as liquid penetrant and dye penetrant testing, this method is particularly useful for assessing the surface conditions of large areas of interest, as compared to other nondestructive imaging tests. International Inspection regularly uses penetrant testing to examine large sections of piping for flaws created during their fabrication or as a result of stresses from normal operating conditions. Our technicians employ various types of penetrant as appropriate to the circumstances, including:
- Solvent-removable penetrant for evaluation of small areas under ambient lighting conditions
- Water-removable penetrant for evaluation of large areas under ambient lighting conditions
- Fluorescent penetrant for in-depth evaluation of small areas under dark conditions with black light
Magnetic Particle Testing
This method of nondestructive evaluation employs principles of electromagnetism to detect small imperfections at and just below a subject’s surface. Normally, an unbroken mass of magnetized material has one north pole from which magnetic forces (also known as flux) exit and one south pole into which those forces re-enter in a continuous flow. An interruption (e.g. a fracture) in that magnetized object will create two new poles: an additional south pole to match the original north and an additional north pole to match the original south. The way that the poles at the ends of the material interact with the poles at the fracture causes the flux to leak at the point of discontinuity if perpendicular to the magnetic flux. Our field technicians exploit this tendency for the purposes of nondestructive evaluation.
Inspectors use a handheld device to generate a magnetic field in a ferromagnetic metal; this may be accomplished using a magnetic yoke, prod, or coil as appropriate to the testing circumstances. They then apply ferrous particles once the surface is magnetized. These cluster to the defect, easily indicating its location, shape, and size. Inspectors may perform this method multiple times on the same subject, changing the poles (and thus the flow) of the magnetic field to reveal new indications.
Our field team uses magnetic particle testing on a variety of ferromagnetic subjects such as pressure vessel walls and piping because of its ability to indicate subsurface flaws. The method may be performed using particles rendered in a dry powder, which is easy to use and versatile onsite, or a wet solution, which can yield indications for smaller discontinuities because of its smaller particle size. Either system can use a colored coating for visibility in ambient light or a fluorescent coating for high visibility under black light in a dark environment.
Ultrasonic Testing
Ultrasonic Testing is a method that allows inspectors to image subsurface conditions in a material. Field technicians apply soundwaves to various types of client assets using a transducer and then record both the amount of time they took to bounce back and how strong the returning waves are with a handheld ultrasonic gauge. They can then use this information to determine certain characteristics of the scanned area, including:
- The thickness of elements such as surface materials, coatings, linings, boiler tubes, tank walls, etc.
- The effectiveness of the adhesive bond between two separate components
- The location of subsurface defects such as laminations, porosity, stringers, cracks, etc.
The method can be performed in a few different ways. Longitudinal waves (also referred to as straight beam or compression waves) are sent from the transducer perpendicularly to the surface material. By doing so, technicians can detect flaws directly within the path of the beam, estimate the size of those flaws based on the readings, and collect various thickness measurements. Alternatively, inspectors can use shear waves (also known as angled beam or transverse waves) by orienting the transducer to a calculated angle with the surface before applying the waves. This allows them to image many potential defects along a greater length of material.
International Inspection regularly uses this method to assess the condition of piping elements throughout an inspection area. Ultrasonic testing offers technicians a greater insight into defects that occur deep within a subject than most other nondestructive methods. Inspectors enjoy its versatility as the equipment used is highly mobile, readings require no wait-time for processing, and the method can be performed with limited access to only one surface of the subject.
Industrial Radiographic Testing
Technicians use radiography to obtain highly detailed images of the internal features of a subject. The basic process is fundamentally the same as that of a medical radiography scan; by sending gamma rays from an emitter into a detector with a subject in between them, our inspectors can display the inside of that subject and commit the result to film. Images created this way are essentially projections of the varying density of materials in the rays’ path, as the detector measures the amount of radiation that made it through the subject.
Our inspectors use iridium-192 as a source material, which emits less radiation than the other isotope commonly used for industrial radiography, cobalt-60. Even considering the lesser amount produced by the iridium source, the radioactivity associated with this method requires 40ft of clearance in every direction to ensure the safety of anyone not wearing appropriate personal protective equipment (PPE). This safety factor sometimes requires the evacuation of the affected area, which can interrupt daily operations if inspections are being performed outside of a planned shutdown. One of the main limiting factors of this technique is that the test cannot be performed if inspectors have access to only one surface of the area, as the detector must be positioned across from the emitter to capture an image.
This method proves a valuable tool to our technicians, as they employ radiography to search for any manner of defect ranging from fractures to corrosion. The field team regularly uses it to assess the condition of boiler tubes and other piping. Furthermore, clients in the construction, petrochemical, and geophysical industries value our radiography services because of their applications in concrete scanning. Although it takes most NDE providers several hours to yield usable images because they have to send data to a remote darkroom for developing, International Inspection brings mobile darkrooms to every radiography job to quickly process images and produce immediately interpretable results.
Ancillary NDE Capabilities
In addition to the specific nondestructive methods we perform, International Inspection also offers a variety of capabilities to supplement our evaluation services. Should the scope of our inspection prove these services to be relevant, our field team can also perform:
Weld Testing
Our inspectors can apply any of the NDE methods listed above to the inspection of welded joints onsite and the qualification of welders in our lab. We perform weld inspections in accordance with applicable codes, including ASME, MIL-STD, and AWS. Our certified technicians select the most appropriate nondestructive method of evaluation to detect and characterize deficiencies in welded elements. Their capabilities range from using ultrasonic testing to identify incomplete fusion in the repair weld of a boiler’s floor tubes to using magnetic particle testing to reveal a cold crack in the lap joint of a tank wall and many more.
Rope Access
Inspection scopes often include areas of interest that technicians cannot access from the ground, such as ceilings on tall structures, ship hulls, and cell towers. While scaffolding can get inspectors close enough to examine their subjects, this solution is expensive to clients and not completely safe for personnel. International Inspection retains a contingent of rope access technicians who are thoroughly trained to safely administer the above NDE methods while suspended in the air. The efficiency they deliver when inspecting otherwise difficult-to-access areas can save clients significant amounts of time and expense.
Contact International Inspection today if your company needs nondestructive evaluation services from a qualified provider. Our expert team of field technicians can meet your specific needs.